Explain the principle and difference of multiple directional
Hydraulic valves are used to control the flow of oil in a hydraulic system or to regulate its flow and pressure.
The directional control valve is a kind of hydraulic valve, which uses the replacement of the flow passage to control the flow direction of the oil.
The unidirectional directional control valve is a directional control valve that only allows airflow in one direction, such as check valves, shuttle valves, double pressure valves, etc.
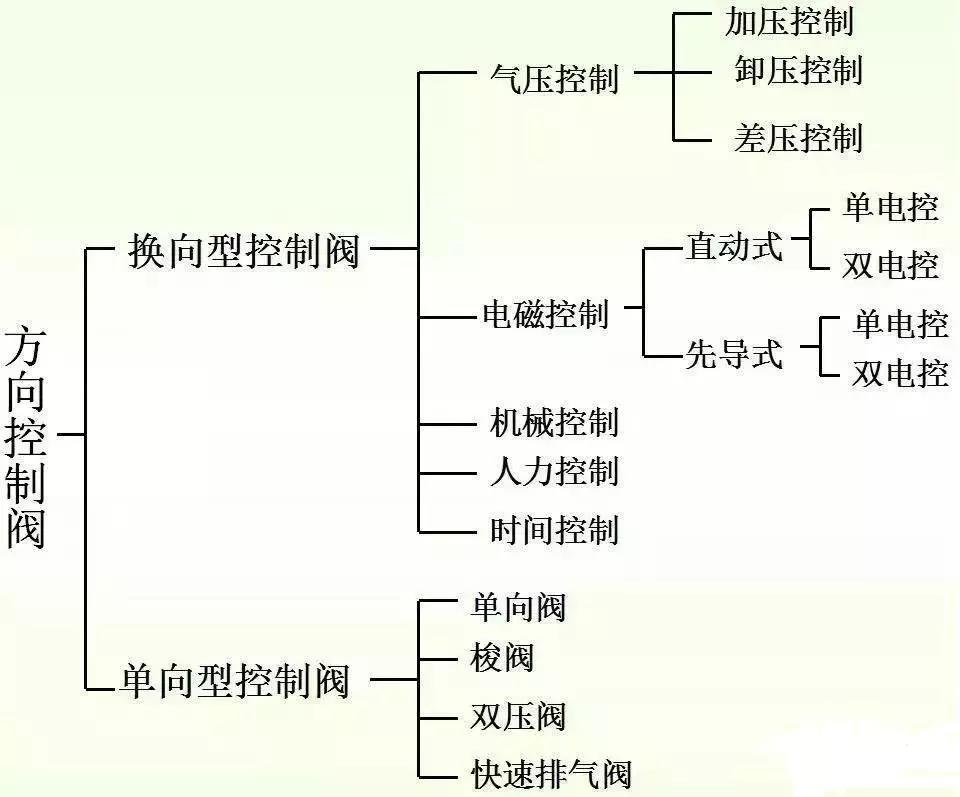
One-way directional control valve
一、Check valve
A check valve is a valve in which the airflow can only flow in one direction and cannot flow in the opposite direction. Check valves are often combined with a throttle to control the speed of the actuator.
1. Composition: valve body, valve core, spring, etc.
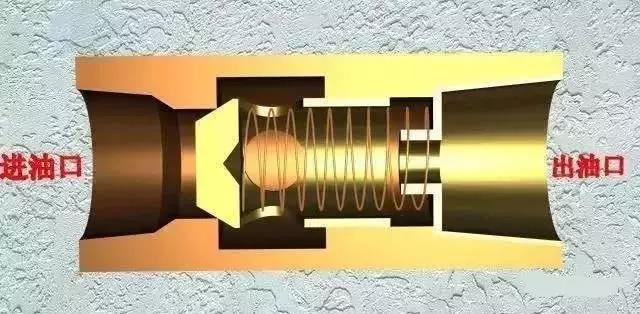
2. Function: Only the liquid flow is allowed to flow in one direction, and the reverse direction is cut off.
3, working principle: forward guidance, reverse cutoff.
4. Application: It is often installed at the outlet of the pump. On the one hand, it prevents the pressure shock from affecting the normal operation of the pump. On the other hand, it prevents the system oil from flowing back to the fuel tank when the pump is not working. It is used to separate the oil circuit to prevent high and low voltage interference.
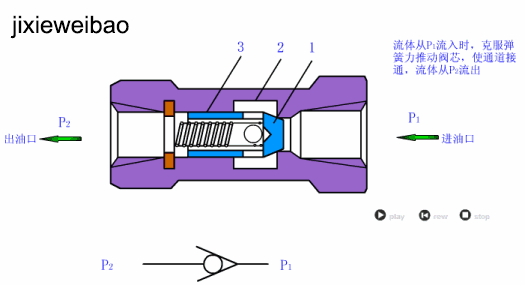
二、Hydraulic control check valve
The pilot operated check valve is a valve that relies on the control of fluid pressure to allow the check valve to flow in the opposite direction. This type of valve occupies a more important position in the hydraulic support equipment of coal mine machinery.
The difference between the hydraulic control check valve and the ordinary check valve is that there is one more control oil circuit K. When the control oil circuit is not connected to the pressure oil, the hydraulic control check valve works like a normal check valve, and the pressure oil It only flows from the inlet port to the outlet port and cannot flow in the opposite direction.
When the control oil circuit has a control pressure input, the piston ejector rod moves to the right under the action of the pressure oil, and the check valve is opened to open the check valve to make the inlet and outlet ports open. If the oil outlet is larger than the oil inlet, the oil can flow in the opposite direction.
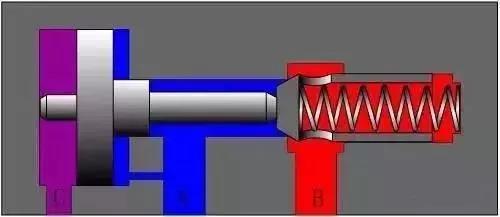
1. Composition: ordinary check valve + small piston cylinder internal leakage type and external leakage type.
2, working principle:
a. No control oil, same as ordinary check valve
b. When the oil is controlled, it can flow in both forward and reverse directions.
3. Application: a. Maintain pressure. b. "Support" of the hydraulic cylinder. c. Realize the locking of the hydraulic cylinder. d, large flow of oil. e, as a charge valve. f, combined into a reversing valve.
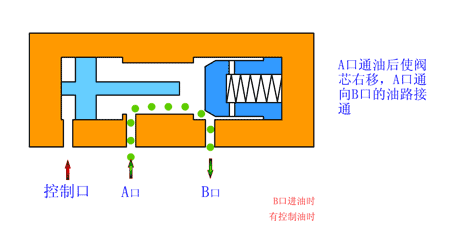
Directional valve
The directional control valve is a directional control valve having two or more flow forms and two or more ports. It uses the valve core to make relative movement in the valve body hole, so that the oil path is turned on or off to change the oil flow direction. It is a valve that realizes the communication, cutting and reversing of hydraulic oil flow, as well as pressure unloading and sequential action control.
Classification of the reversing valve:
According to the structure, it can be divided into slide valve type, rotary valve type and ball valve type. The number of main oil passages connected by the valve body can be divided into two-way, three-way, four-way and the like. According to the working position of the valve core in the valve body, it can be divided into two, three, four, and the like. According to the way of operating the spool, it can be divided into manual, motorized, electromagnetic, hydraulic, and electrohydraulic.
First, the manual reversing valve
The manual reversing valve is a manual lever operated directional control valve that acts in both the commutation (changing the flow direction) and the switch (turning the flow on or off) in the hydraulic system.
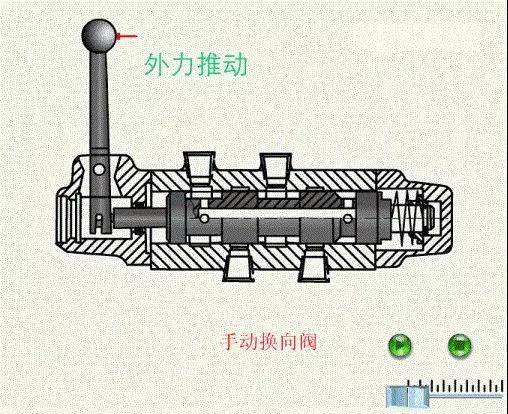
Second, the motorized reversing valve
The motorized reversing valve, also known as the stroke valve, is mainly used to control the stroke of the mechanical moving parts, and the movement of the spool is forced by the iron or cam mounted on the table to control the flow direction.
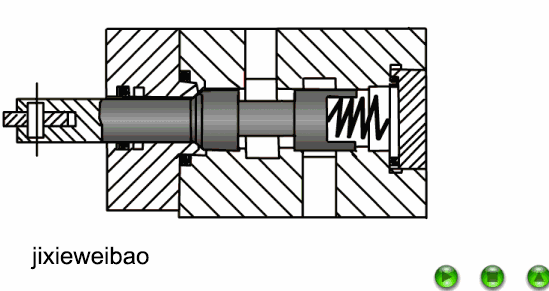
Third, the electromagnetic reversing valve
The electromagnetic reversing valve uses the electromagnet suction to push the spool to change the working position of the valve. It changes the direction of the flow control and changes the position of the hydraulic directional control valve.
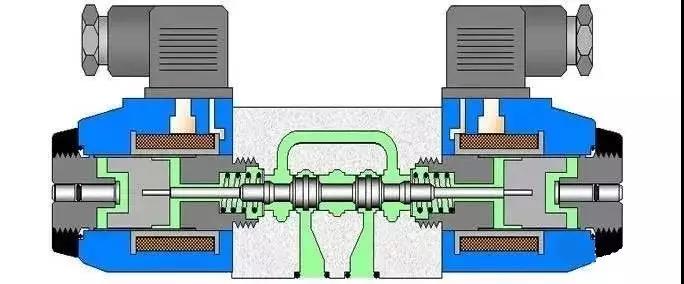
Since the hydraulic thrust of the hydraulic directional control valve can be large, the main valve can be made large, allowing a larger flow rate to pass. This allows a larger electrofluid to be used to control a larger flow.
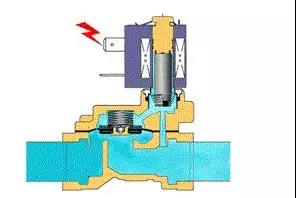
Fourth, other valves
Classification according to the working position of the valve The working position of the valve is called “position”, and several valves that switch the working position are called “several” valves. There are often two-position valves and three-position valves. The position at which the valve is in the absence of a control signal or is operated is referred to as the zero position.
The interface of the valve (including the exhaust port) according to the number of interfaces of the valve is referred to as "on", and the interface of the valve includes the inlet, outlet and exhaust ports, but does not include the control port. Common valves are two-way, three-way, four-way, and five-way.
(1) Two-position two-way reversing valve
Principle: It is a combination of direct motion and pilot type. When there is no pressure difference between the inlet and the outlet, after energization, the electromagnetic force directly lifts the pilot small valve and the main valve closing member upward, and the valve opens.
When the inlet and outlet reach the starting pressure difference, after the energization, the electromagnetic force leads the small valve, the pressure of the lower chamber of the main valve rises, and the pressure of the upper chamber drops, so that the main valve is pushed upward by the pressure difference; when the power is off, the pilot valve uses the spring The force or medium pressure pushes the closure and moves down to close the valve.
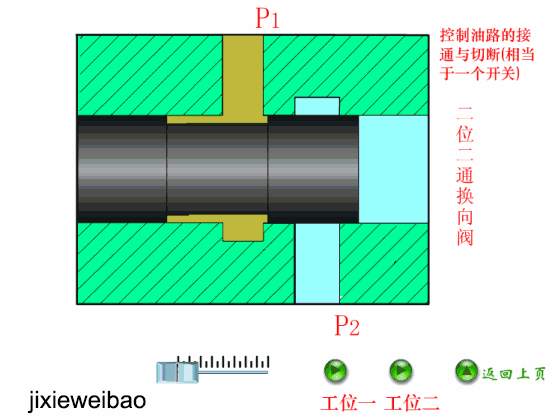
(2) Two-position four-way reversing valve
The two-position four-way reversing valve is an integrated reversing control device that uses a DC motor to drive the spool to move the oil supply pipe or switch the oil supply direction; even under severe working conditions (such as low temperature) Or high viscosity grease), the action is still quite reliable.
The valve is suitable for the dry and thin oil centralized lubrication system with a nominal pressure of 40 MPa or less and the main branch pipeline of the hydraulic system. It can also be used as two-position four-way, two-position three-way and two-position two-way.
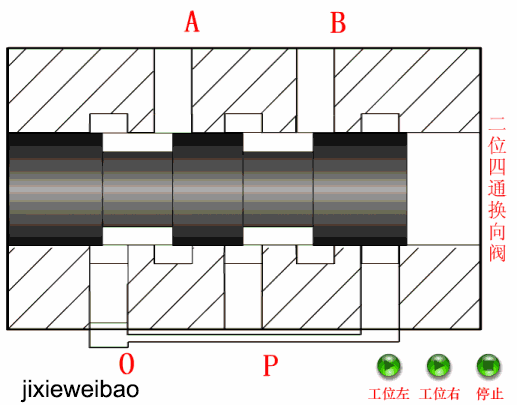
(3) Three-position four-way reversing valve
Three-position four-way reversing valve: It means that the valve has three working positions, there are four ports (generally two in and two out), which are represented by P, T, A, B respectively, P is the oil inlet, T is back The oil port and AB are respectively connected to the upper and lower chambers of the actuator, and the valve is in the neutral position at the natural position. The structure of the valve is shown in the diagram:
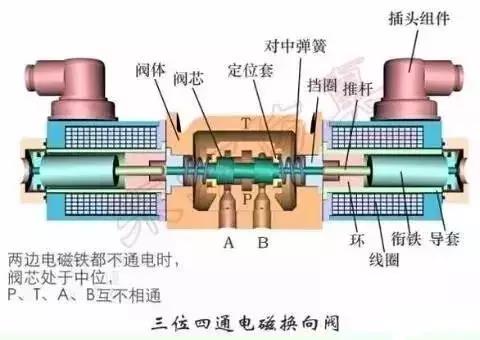
According to different commutation methods, it can be divided into three types: electromagnetic type, electro-hydraulic type and manual type. The working principle is as follows:
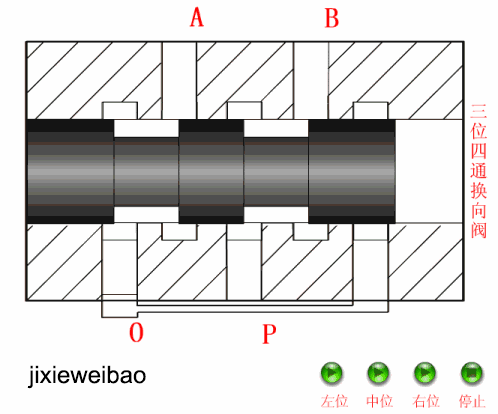
(4) Three-position four-way electromagnetic reversing valve
The three-position four-way electromagnetic reversing valve has three disadvantages: large volume, no anti-vibration, poor waterproof performance, and its use environment is greatly limited.
The new three-position four-way electromagnetic reversing valve has made significant improvements in structural design, process design and material selection. The volume is 1/3 smaller than the traditional solenoid valve, and it has strong anti-vibration and waterproof performance.
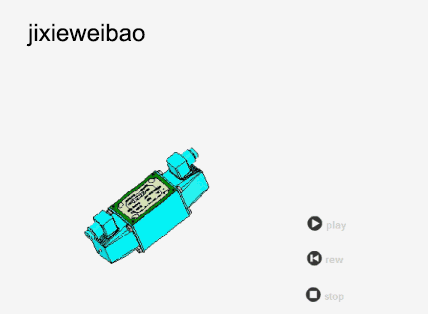
(5) Three-position five-way reversing valve
The three digits mean that the reversing valve has three positions, the left position, the middle position, and the right position. The five links indicate that there are five interfaces, that is, there are five ports on the solenoid valve connected to the system piping. Its working principle is as follows:
Since the hydraulic thrust of the hydraulic directional control valve can be large, the main valve can be made large, allowing a larger flow rate to pass. This allows a larger electrofluid to be used to control a larger flow.
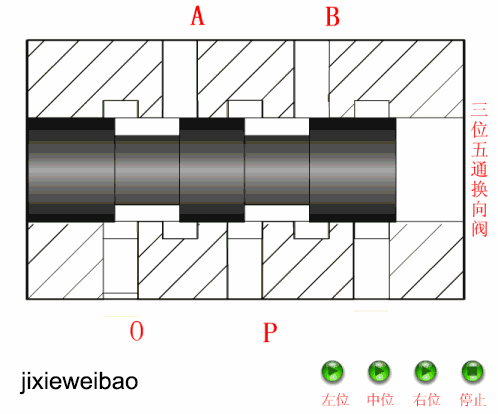
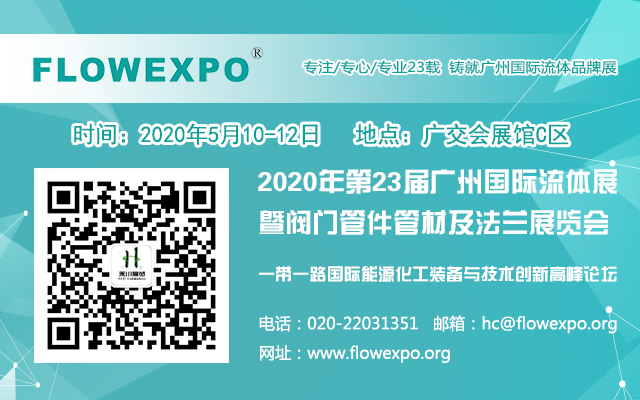
Pre:The compound annual growth rate of the global industrial val Next:Talk about the valve's "running and dripping" Back